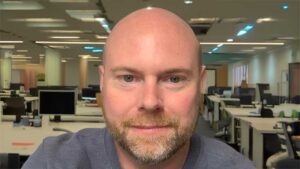
Bryan Winquist is a seasoned Environmental Health and Safety Manager at Tyson Foods, where he leads with a strong commitment to safety and sustainability.
With a background as a firefighter and paramedic, Bryan brings a wealth of experience in emergency response and risk prevention to his role. He holds a degree in Biological Sciences from the University of Wisconsin, which underpins his expertise in environmental health.
Beyond his corporate responsibilities, Bryan Winquist is deeply involved in sustainable agriculture at Nubian Meadows Farm in Somerville, Tennessee. Here, he practices eco-friendly farming and raises Angus cattle, integrating his passion for environmental stewardship with his agricultural ventures.
A lifelong learner and active member of the National Fire Protection Association, Bryan continuously enhances his knowledge and skills to better serve his community and the environment. His work exemplifies a dedication to creating safer, healthier workplaces and a more sustainable world.
What initially drew you to a career in environmental health and safety?
My interest was sparked during my time as a firefighter and paramedic. I saw the direct impact of preventive measures and the consequences of neglecting them. This experience made me realize the potential of proactive safety management in saving lives and improving outcomes, which led me to pursue this field.
How do you balance the demands of being a safety manager at Tyson Foods with managing your farm, Nubian Meadows?
Balancing these responsibilities requires strict time management and prioritization. Mornings are often dedicated to farm duties, while afternoons are for my role at Tyson Foods. Technology also plays a big role, allowing me to monitor farm operations remotely and maintain constant communication with my team at Tyson.
Can you describe a challenging situation where you successfully implemented a safety solution?
One significant challenge was integrating a new safety protocol across multiple departments at Tyson Foods. The key to success was in thorough training and transparent communication. We held cross-departmental meetings to ensure everyone understood the benefits and procedures, which greatly facilitated a smooth implementation.
What strategies do you find most effective for promoting safety awareness among employees?
I believe in leading by example and making safety a core value rather than just a requirement. Regular training sessions, interactive safety drills, and open discussions about safety concerns help foster a culture where safety is everyone’s priority. Recognizing and rewarding safe behavior also reinforces its importance.
How has your approach to safety management evolved over the years?
My approach has become more holistic, focusing not just on preventing accidents but also on promoting overall well-being. This includes mental health, ergonomic improvements, and even environmental sustainability, understanding that a healthy environment contributes to safer workspaces.
What trends do you see shaping the future of environmental health and safety in the agricultural sector?
Technology will continue to play a huge role, especially through the use of data analytics for risk assessment and the integration of IoT devices for real-time monitoring. Additionally, there’s a growing emphasis on sustainable practices that reduce environmental impact and enhance worker safety simultaneously.
What advice would you give someone starting their career in environmental health and safety?
Stay curious and keep learning. This field is constantly evolving with new challenges and technologies. Networking with other professionals and joining relevant associations can provide valuable insights and opportunities for growth. Also, be prepared to advocate for safety changes, which requires not just technical knowledge but also strong communication skills.
What are some of the biggest obstacles you’ve faced in implementing environmental health and safety measures in both corporate and farm settings?
One of the biggest obstacles is the initial resistance to change, especially when introducing new technologies or protocols that alter long-standing practices. Both in the corporate environment at Tyson Foods and on my farm, overcoming this involves clear communication about the tangible benefits and training to ensure everyone is comfortable with new systems. Another challenge is balancing cost with benefit, as upfront investments can be substantial, but I focus on long-term gains in safety, efficiency, and sustainability to justify these expenses.
How do you ensure compliance with safety regulations across different teams and locations?
Ensuring compliance involves a combination of regular training, clear communication of expectations, and a robust auditing process. I implement consistent standards across all teams and locations, supported by regular inspections and real-time monitoring where possible. Engaging team leaders to champion safety practices within their groups is also crucial, as it helps maintain high standards and accountability at every level of the organization.
Looking ahead, what new initiatives or projects are you excited about at Tyson Foods or on your farm?
At Tyson, we are exploring advanced automation technologies to enhance safety in our processing plants. On my farm, I’m excited about expanding our use of solar energy, aiming to power more of our operations entirely by renewable sources. These projects not only push us toward greater efficiency and safety but also align with our commitment to sustainability.
Read more:
Q&A with Bryan Winquist: Insights on Safety, Sustainability, and Leadership