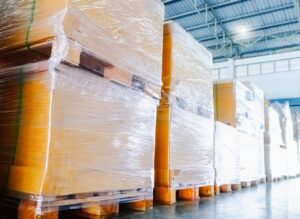
Shipping damage might feel like just another cost of doing business, but the truth is, it adds up. Between refunds, replacements, delays, and unhappy customers, the impact often stretches far beyond the broken box itself.
And it’s not just about the product. It’s the knock-on effect — the emails, the lost time, the second delivery run. Over time, that eats into more than just your stockroom. It wears down trust. It drains energy. For food and drink suppliers in particular, where timing and condition are everything, one weak link in the packaging can turn a routine job into a scramble.
Yes, tougher boxes help. But they’re only part of the fix. It’s often the small choices — the wrap you use, the way pallets are stacked, the gap you forgot to fill — that make all the difference.
So, what’s going wrong between dispatch and delivery? More often than not, it comes down to one thing: the way items are packaged and secured for travel.
Let’s look at practical ways you can reduce shipping damage — and the simple changes that make a big difference.
It’s Not Just About the Box — Securing the Load Matters
Many business owners focus on choosing the right box for the job — which is smart. But damage often doesn’t happen inside the box. It happens when boxes move, slide, tip, or collapse under pressure.
This is where outer protection comes in. One of the simplest and most effective tools is pallet wrap. It secures entire loads together, reducing the risk of movement and impact during handling. If you’re not using enough of it — or the right type — items can shift in transit, even on short journeys.
There are different wraps to suit different weights and climates, from standard cast film to high-performance machine wrap. It’s worth testing a few options with your supplier to find the best fit for your specific shipments.
Use the Right Materials for the Job
Some items need more protection than others. Liquids, glass, electronics, and perishables don’t just need cushioning — they need structure.
Void fillers like paper or air pillows can help, but in transit-heavy industries, it pays to invest in materials built for the job. For example:
Edge protectors or corner boards prevent crushing under weight or tight strapping.
Anti-slip sheets keep loads stable on pallets.
Strapping systems hold boxes or products firmly in place.
These aren’t only for big operations. Many small and mid-sized companies have started using the same methods couriers and warehouses rely on — because fewer breakages mean fewer headaches.
Packing Too Much or Too Little? Both Can Cause Damage
Some packers go overboard. Others hold back. Either way, things tend to go wrong.
If you’re cramming items into a box just to be safe, pressure builds. Sides bulge. Seals strain. Eventually something gives. But loosen things up too much, and you’ve got contents rattling inside like they’re on a rollercoaster. Empty space can be just as risky as overstuffed corners.
It’s not about using more padding or stronger tape — it’s about getting the fit right. If there’s a gap, fill it with something that absorbs shocks without adding weight. If your item’s fragile, don’t double the tape — use a sturdier box. A snug, steady fit beats brute force every time.
Staff and Couriers Can Make or Break Your Packaging
It’s one thing to have the right materials — it’s another to use them properly.
If your dispatch team is rushed or undertrained, even great packaging can go to waste. Shortcuts like not wrapping pallets tightly, skipping edge guards, or using the wrong-sized boxes often lead to repeat damage.
It’s worth running a short packaging workshop internally, or even asking your supplier for a visit. A 20-minute refresher on packing technique can reduce breakage by a surprising amount.
Also, talk to your couriers. Ask how they handle your goods — and if they’ve noticed issues. If your shipments are being stacked sideways, or handled roughly, they may be able to recommend different loading methods or vehicle options.
Is Your Packaging Still Doing the Job? Time to Check
What worked last year may not be the best fit now. Products change. Supply chains change. Couriers change.
Set a time every quarter to review breakage reports and returns. Is there a pattern? Is one product always arriving damaged? Is one courier responsible for most complaints? Are seasonal conditions affecting certain packaging types?
This kind of audit can reveal problems you didn’t even know existed — and help you fix them before they cost you more.
Get the Basics Right — and the Rest Follows
Preventing breakages doesn’t need a full overhaul. It doesn’t mean adding steps or slowing things down. Often, it’s about catching what’s been overlooked — and fine-tuning the process.
Revisit the basics. Wrap better. Pack tighter. Use materials that do more than just tick boxes. With just a bit more thought at the prep stage, you’ll avoid awkward surprises later on. And your customers? They’ll barely notice — which is exactly the point.
Read more:
Reducing Shipping Damage: Smarter Packaging Choices That Work